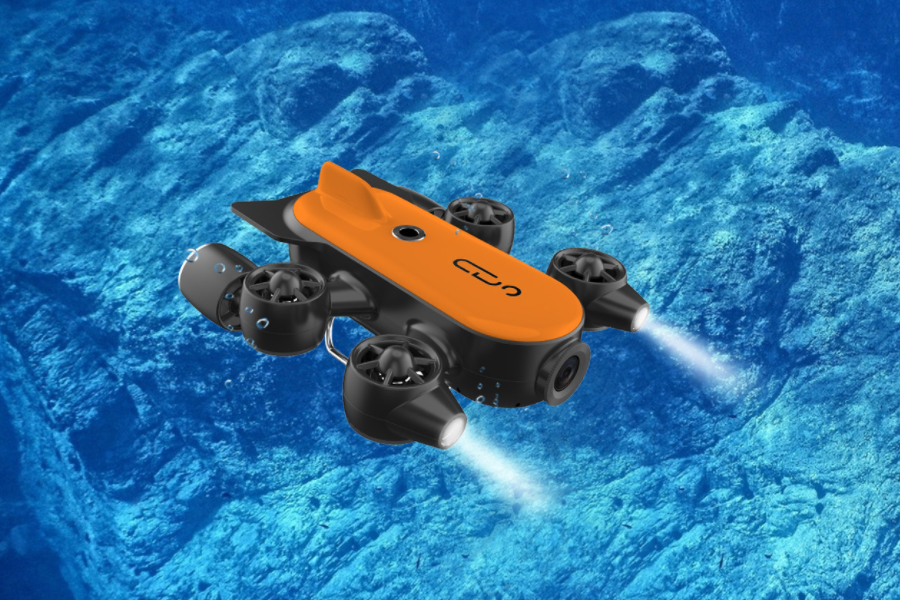
In the manufacture of injection molds, the exhaust of injection molds is a very important part.The exhaust of the injection mold can represent the overall structure of the injection mold to the greatest extent.Even if an excellent injection mold does not have good exhaust, it is impossible to produce a product of stable quality. A good injection mold should have good airtightness and ensure the free discharge of gas, rather than the gas being highly compressed.So what is the standard for injection mold exhaust?Let me introduce it to you next.
It is necessary to make a full-circle exhaust structure as much as possible, and the depth is within the plastic overflow value. The full-circle exhaust is the best, but it is necessary to leave 1/2 of the steel to compensate for the pressure on the clamping line.If the PL surface is irregular and cannot be exhausted all around, the better way is to use a 12mm wide exhaust slot to the master mold. The gas must eventually be exhausted to the atmosphere. Use a flat-bottomed milling cutter to process the exhaust as much as possible. Slots, if you must use a spherical milling cutter, you must calculate clearly that the processing depth is consistent with the depth processed by the flat bottom. The length of the vent sealant is the most easily overlooked by most people, and it is related to the proper venting problem. , On this issue, there are a lot of different size regulations. The material supplier’s specifications range from 3 to 5mm, and experience has shown that if the length is greater than 3mm, it will no longer play a good role. Therefore, for safety reasons, we set the standard as 3mm, the exhaust depth depends on the molding material, if in doubt, please refer to the processing specifications.
One of the most common misconceptions is that too much exhaust will cause the front to blow. In fact, the opposite direction is correct. Unreasonable exhaust requires excessive pressure. When the gas is allowed to escape, the rubber will go out with the gas. The only thing that causes excessive exhaust and blows the front is that the air groove is too deep.Usually try to use all the thimble to exhaust. This is particularly important for large plastic parts. Of course, this is also determined by the diameter of the thimble. If this is not possible, it is necessary to grind the surface to exhaust, use a suitable length and depth, and Slow down the thimble fitting clearance, and the runner, especially the large or long runner, must be vented.
Another common problem is that when the parts cannot be exhausted all around, the last and the second last filling positions must be considered, and the two positions must be exhausted.Deep bone position, column position, small needle dispensing position or thin glue position must be specially considered for exhaust, or use flat thimble, semi-needle structure or exhaust steel, or even use vacuum exhaust device.
A part cannot be exhausted too much, although the parting line can be done, this will bring the following problems related to exhaust: there is not enough steel to bear the pressure on the parting line, and the exhaust is pressed on the parting surface ; The best exhaust will eventually disappear. After a certain material cycle, if there is not enough steel to compensate the pressure on the parting line, the injection mold will snap together and the air groove will wear out. The parting line should be avoided The reduction of the clamping part of the injection mold is one of the biggest problems encountered by the large mold.For the injection mold of the front and rear mold inserts, the front and rear mold core materials cannot be closed before the mold base parting surface is closed.The correct way is to use pressure-resistant blocks to simultaneously close the molds between the AB plates of the mold base.
Link to this article:The standard of injection mold exhaust