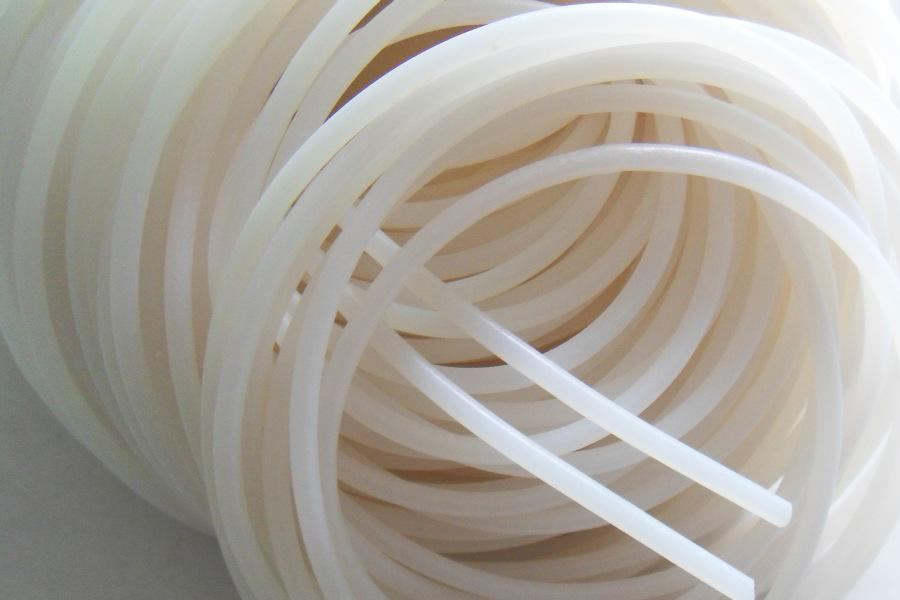
Please follow the editor’s footsteps and analyze what needs to be done to make “high-end atmosphere” plastic molds.
Appearance, size and fit of molded products
- The product surface is not allowed to have defects: lack of material, burnt, white surface, white lines, peaking, blistering, whitening (or cracking, breaking), baking and wrinkling.
- Welding traces: Generally, the length of circular perforation welding traces does not exceed 5mm, and the length of special-shaped perforation welding traces does not exceed 15mm, and the strength of the welding traces can pass the functional safety test.
- Shrinkage: Shrinkage is not allowed in the obvious area of the appearance, and slight shrinkage is not allowed in the inconspicuous area (no dents).
- Generally speaking, the flatness of small products is less than 0.3mm. If there are assembly requirements, the assembly requirements must be guaranteed.
- There should be no air pipes or material flowers on the appearance, and the product should generally not have air bubbles.
- The geometric shape and dimensional accuracy of the product should meet the requirements of the official and effective plastic mold drawing (or 3D file). Product tolerances should be based on tolerance principles. The shaft size tolerance is a negative tolerance, and the hole size tolerance is a positive tolerance. Customers have requirements according to their requirements.
- Product wall thickness: The product wall thickness is generally required to be the average wall thickness, and the non-average wall thickness should meet the requirements of the drawing. According to the characteristics of the plastic mold, the tolerance should be -0.1mm.
- Product matching: the case and the bottom case are matched: the surface misalignment is less than 0.1mm, and there should be no scratches. For holes, shafts and surfaces with matching requirements, the spacing and use requirements must be matched.
The appearance of the plastic mold
- The nameplate of the plastic mold is complete, with clear text and neat arrangement.
- The nameplate should be fixed on the mold foot near the template and the reference corner. The nameplate is reliable and not easy to peel off.
- The cooling water nozzle should be made of plastic block water nozzle. If the customer has other requirements, please follow the requirements. 4. The cooling water nozzle should not protrude from the surface of the mold base
- The cooling water nozzle needs to be reamed. The counterbore diameter is 25mm, 30mm and 35mm. The holes are chamfered and the chamfers should be the same. .
- The cooling water nozzle should be marked with inlet and outlet.
- Mark English characters and numbers should be greater than 5/6, and the position should be 10mm directly below the faucet. The handwriting should be clear, beautiful, neat and evenly spaced.
- Plastic mold accessories should not affect the lifting and storage of plastic molds. During installation, exposed cylinders, faucets, pre-reset mechanisms, etc., should be protected by supporting feet.
- The support legs should be fixed on the base of the plastic mold with screws passing through the support legs. Overlong support legs can be fixed on the base of the plastic mold with machined external threaded posts.
- The size of the ejector hole of the plastic mold should meet the requirements of the designated injection molding machine. Except for small plastic molds, one center cannot be used for ejection.
- The positioning ring should be fixed and reliable. The diameter of the ring is 100mm and 250mm. The positioning ring is 10-20mm higher than the bottom plate. Unless the customer requires otherwise.
- The overall size of the plastic mold should meet the requirements of the designated injection molding machine.
- For plastic molds with orientation requirements, arrows should be used to indicate the installation direction of the front template or the rear template. There should be “UP” next to the arrow. The arrows and text are yellow, and the font height is 50 mm.
- The surface of the mold base should not have pits, rust marks, excess rings, water vapor in and out, oil holes, etc., and defects that affect the appearance.
- The plastic mold should be easy to hoist and transport, and the various parts of the plastic mold must not be disassembled during the hoisting process, and the hoisting ring must not interfere with the faucet, oil cylinder, pre-reset rod, etc.
Link to this article:How do we make a "tall" plastic mold?