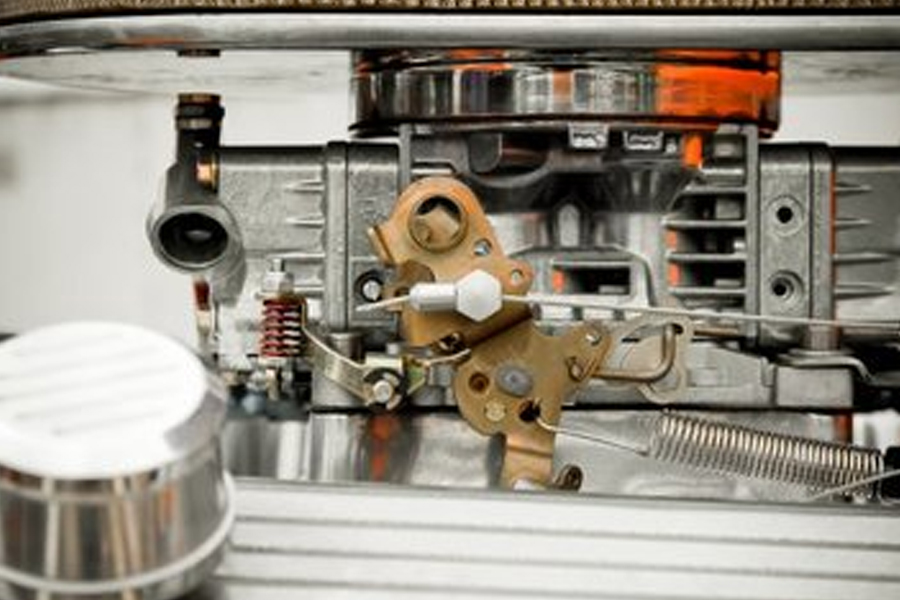
Analyze the cause of flow marks on the surface of injection mold products
This term explains the linear trajectory on the surface of the molded product, which shows the direction of melt flow. Two fault analysis and troubleshooting methods The flow of molten material causes the surface of the plastic part to take the shape of annual rings centered on the gate. Wave traces. The temperature of the injection mold and the nozzle can be increased respectively, the injection speed and filling speed can be increased, and the injection pressure, holding pressure and pressurizing time can be increased.
A heater can also be installed at the gate to increase the local temperature of the gate. The area of the gate and the runner can also be appropriately increased. The cross-section of the gate and the runner should be round in order to achieve the best filling effect. However, if the gate is placed in a weak area of the plastic part, a square section should be used.
In addition, there should be a large cold hole at the bottom of the inlet and the end of the runner. The influence of material temperature on melt flow properties is more important. Pay more attention to the size of the cold hole, the location of the cold hole must be set in the melt. The end of the flow direction is along the inlet. The melt in the flow channel does not flow smoothly, so a spiral wave-like flow mark is formed on the surface of the plastic part.
When the melt flows from the narrow section of the runner into the cavity of the larger section, or when the runner of the injection mold is narrow and the finish is poor, the flow may become turbulent, resulting in a wave-like flow on the surface of the spiral plastic part. In this regard, the injection speed can be appropriately reduced, or the injection speed can be controlled to be slow, fast, or slow. The gate of the injection mold should be placed in the thick wall or directly on the side of the wall. The gate type is preferably a handle, a sector or a diaphragm. It is also possible to appropriately increase the runner and gate cross-sections to reduce flow resistance.
Volatile gas forms a cloud-like wave-like flow mark on the surface of the plastic part. When using ABS or other copolymer resin raw materials, if the processing temperature is high, the volatile gas generated by the resin and lubricant may form cloud-like wavy flow marks on the surface of the plastic part. In this regard, the temperature of the injection mold and barrel should be appropriately reduced, the exhaust conditions of the injection mold should be improved, the material temperature and filling rate should be reduced, and the gate section should be appropriately increased. The type of lubricant should be changed or the amount of lubricant should be reduced.
Link to this article:Analyze the cause of flow marks on the surface of injection mold products