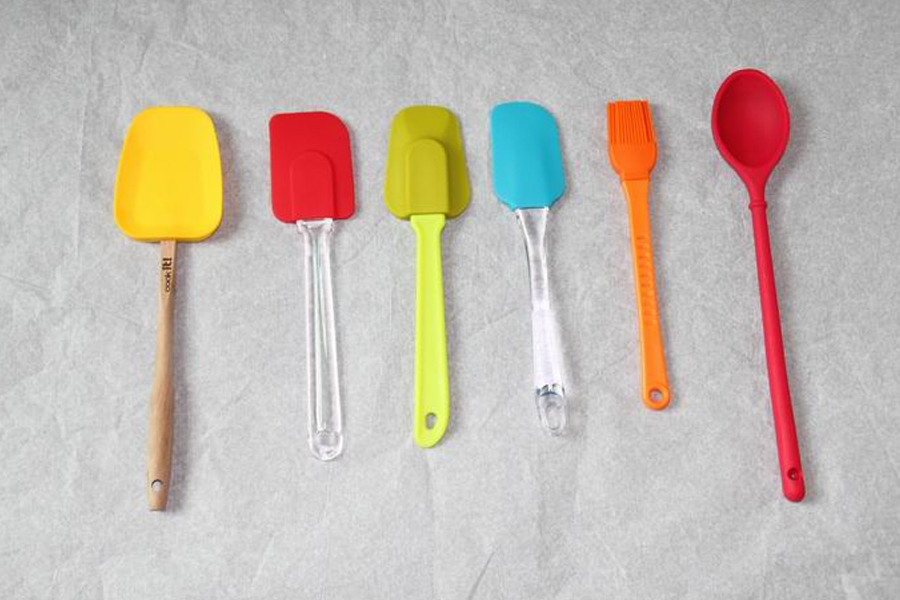
In order to improve the competitiveness of the factory, strive to shorten the manufacturing cycle and reduce the manufacturing cost is the goal of all mold manufacturers.Nowadays, the traditional “manual mold making” has been replaced by automated numerical control equipment, and more and more plastic mold manufacturers have begun to pay attention to and introduce automated production systems and equipment.
Traditional manufacturing processes are more sensitive to the introduction of automation. On the surface, the use of robots can reduce the number of operators and save labor costs. However, the actual cost of purchasing a robot is far greater than the labor cost.So how to understand the contribution of automation to reducing costs?We need to analyze the occurrence of huge and intangible costs and the risk of loss of intangible assets.
- 1) The use of automation reduces the requirements for operating skills, greatly improves productivity, and gives full play to the processing efficiency of the machine tool.
- 2) The actual processing time per week is up to160Hours, greatly enhance economic efficiency.
- 3) The machine tool will only create economic benefits when it is processed.reduce costs,increase income.
- 4) To get the best return on equipment investment, higher safety production and more consistent products.
- 5) The use of automation avoids manual intervention in processing, resulting in higher quality and fewer waste products.
Link to this article:Why do mold manufacturing plants need to invest in automation equipment?