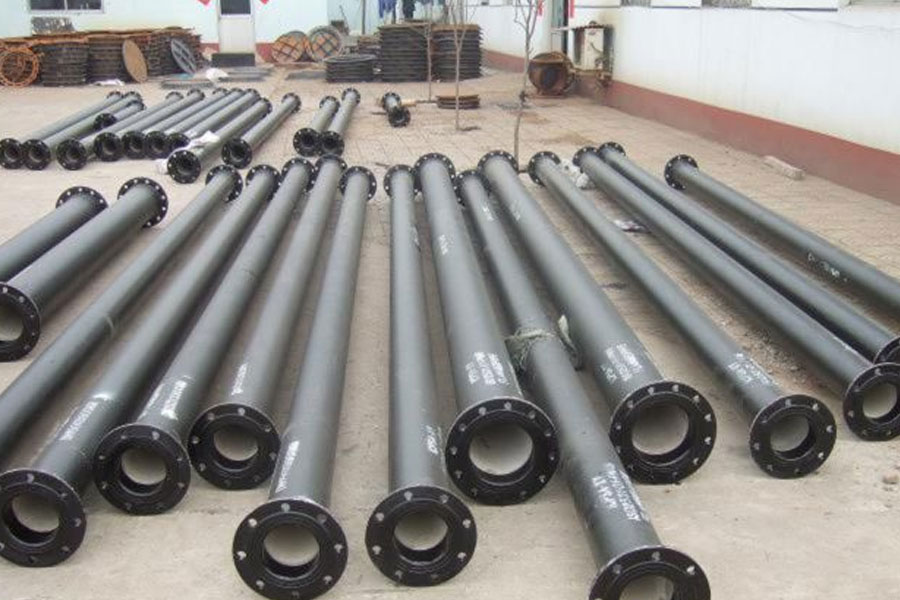
With the rapid development of my country’s economy, the application of injection molds in various industries has become more and more mature. Many plastic parts of products need to use injection molds, and the quality and service life of injection molds affect the production cost of enterprises. Therefore, it is very important to improve the quality and maintenance of injection molds to improve the service life of injection molds. So what factors will affect the quality of injection molds and how to maintain injection molds?
Injection molds will affect the final injection mold quality in terms of raw materials, design, processing technology, etc. The specific manifestations are as follows:
1. Mould steel
Steel is the decisive factor of mold quality, and choosing a reasonable steel is the top priority.The criteria for selecting steel are:
①Requirements for injection molding materials
Different plastics should use different steels, such as high polishing requirements, corrosion resistance requirements, etc.;
②Price
The steel can be used as long as it is more expensive; considering the cost factor of the mold, the mold steel should be selected corresponding to the mold life to prevent unnecessary waste; the life of the general P20 material is about 30; 2738 There is no problem if the data is 50, H13/2344 is usually more than 80-100 million, which can be selected according to the situation;
③Appearance treatment
The appearance of the mold is also very important.Nitriding can enhance the surface hardness of the steel and effectively extend the life of the mold; electroplating can usefully modify the mold steel. For some plastic parts that require high brightness and corrosion resistance, electroplating can be used to enhance and improve the function of the steel.
2. Structural design
The mature mold structure not only considers the characteristics of product materials, shortening rate, molding temperature, elastic tensile deformation coefficient, etc., but also considers the cooling water circuit and the speed of mold opening and closing.A reasonable mold structure can effectively extend the life of the mold and ensure the smooth production of the mold, improve efficiency, and reduce costs.
3. Mold processing
If a worker wants to do well, he must first sharpen his tools.The organization of the mold process is particularly important. A reasonable process organization can speed up the production cycle, shorten the processing time, and effectively save costs.And more importantly, accurate and reasonable processing can ensure the stability and extended life of the mold during the production process.Some processing errors will cause mold welding, no matter how good the welding is, it is a loss to the mold; other poor processing may also affect the mold operation, reduce the mold life, and cause the mold to appear in the production process Pull and even break.
4. Standard Parts
The one that determines the capacity of the bucket is the lowest piece of wood.We all understand this truth, but we often fail to notice it when we do it.The same is true for molds. Although standard parts are not directly involved in forming, they control the operation of the entire mold.Good standard parts should be wear-resistant, hard enough, high precision, and not suitable for deformation.There is a big price difference between standard parts of different brands, so don’t blindly bargain the price when making molds.
5. Butt bump (flying model)
It depends on the experience of mold fitter. The seemingly simple job is the most technical job.The first thing that messy molds look at is this skill.The flat mold is the simplest, and the fractal surface only needs to be free of flash and error.For example, car parts molds are very troublesome, not only the fractal surface is relatively irregular, but also often contains multiple sliders and top blocks.The other problems of the mold can be improved and perfected through the bumping together, so it is a comprehensive operation.
6. Polishing/Leather Grain
The polishing of the mold is the final link in the production of the mold.Polishing is directly reflected on the plastic parts, so this is the most decent job.Polishing can also help and compensate for the action of the mold, especially for demolding.Often, some molds are not produced smoothly because of improper lighting, excessive resistance, difficulty in demolding, and even whitening and capping.
7. Mould device
The mold device is just like the assembly machine. Every component and every screw must not make mistakes, otherwise the result will be quite serious. In the light of it, it will lead to product defects and affect the production.Therefore, the work of the installation must be very detailed.During the installation process, pay attention to the cleaning of the mold, especially the waterway and screw holes, and be sure to clean the iron filings inside.
8. Warm runner is still cold runner
This actually has the least impact on the quality of the mold, because the warm runners are generally designated by customers, especially some large customers.Well-known foreign brands do everything in terms of quality or after-sales service, so there is generally no problem in quality.Only some domestic warm runners are very different in quality.In order to save costs and compete for price advantage, a single small business uses some unreliable heating and conduction accessories to simply cause problems.The primary problem of cold runner is how to ensure the balance of injection molding, gate size, injection pressure and so on.
9. Cooling water circuit
Anyone who has experienced mold knows how important cooling is to a mold.Because of the increase in prices and human wages, it is impossible to imagine the profit that does not cut the injection cycle of one second when the product is produced in large quantities.However, speeding up the production cycle will result in an increase in mold temperature. If it is not effectively controlled, it will make the mold too hot to be unable to form, and even cause the mold to deform and become invalid.Therefore, excellent waterway design is particularly important, including the arrangement density, diameter, and mutual links of the waterway.
Maintenance of injection mold
Mold maintenance is primarily maintenance and maintenance during the production process.The mold is like a car, if it is not needed for a long time without maintenance, it may cause the mold to become useless.Therefore, every time the mold is used, a comprehensive maintenance must be carried out, especially the rust prevention of the molding part, and the rust prevention of the main moving parts.Because the mold needs to receive water during the production process, it may sleep on the mold during the installation or disassembly process, so make sure that the mold is dry, and then brush a layer of oil for maintenance.
XNUMX. The use of injection molds
The mold creates value in use, but gradually loses its own value in use. Therefore, the operator must attach great importance to the use of the mold. Generally, the following points should be paid attention to.
- (1) Before use, check whether there are impurities and dirt in each part of the mold. The plastic and impurities remaining in the mold should be scrubbed with cotton yarn, and the sticky materials with strong adhesion should be scraped off with a copper knife.
- (2) Choose the clamping force reasonably, based on the fact that there is no flash when the product is formed. It should not be assumed that the higher the better, it will increase the power consumption and easily damage the transmission parts.
- (3) The transmission parts should be well lubricated, therefore, the lubrication of these parts must be maintained.
- (4) It is not allowed to hit any parts in the mold with heavy objects such as horns to avoid deformation or even damage to the mold.
Second, the maintenance of the injection mold
(XNUMX) Maintenance of cooling water channels
The function of the cooling water channel is to cool down and solidify the plastic parts in the cavity through cooling water, which has a greater impact on the molding process of the plastic parts.
1. The hazards of blockage of cooling water channels
In the long-term work process, the surface of the cooling water channel is prone to deposit scale, dirt, rust, etc., which will reduce the circulation area of the cooling water channel, and greatly reduce the heat exchange between the cooling water and the mold, so that the cooling effect is greatly reduced, which is harmful Very big.
2. Check the blockage of the cooling water channel
The increase of deposits on the surface of the cooling water channel will cause local blockage of the water channel. This can be used to determine the internal condition of the cooling water channel by measuring the flow rate of the cooling water.When measuring, a pressure control valve can be installed between the mold and the cooling water channel. Under the same conditions, the pressure drop of the cooling water through the mold can be measured.From this, the blockage of the cooling water channel can be judged.If the blockage reaches a certain level, it must be cleaned up in time.
3. Cleaning of cooling water channels
Because the design of the cooling water channel is related to the shape of the cavity, its shape is tortuous and inconvenient to disassemble. Therefore, it cannot be cleaned by mechanical methods. It can only be washed with a cleaning agent, and the adhered dirt is removed under the strong impulse of the cleaning agent. .There are many kinds of cleaning agents used, and you can choose to use them.
(XNUMX) Maintenance of injection mold unloading
After the injection mold completes a given production task, it needs to be disassembled from the injection molding machine.When disassembling, carefully remove the residual plastic, and adopt different cleaning methods according to the different properties of different plastics.Generally, soapy water can be used to remove residual plastic and other deposits in the mold, and then the mold is air-dried.If there are rusty spots on the surface of the cavity, they should be removed, polished, and then coated with lubricant for protection, and then placed in the inventory.
Three, the failure of the injection mold and its elimination
In the working process of injection molds, there will always be more or less failures, which will adversely affect product quality, productivity, molds, etc., which will be described below.
(XNUMX) Mold deformation and its elimination
Mold deformation refers to the excessive elastic or plastic deformation of the mold during the work process, which makes the mold unable to work normally or the product quality is unqualified. The reasons and troubleshooting methods are as follows.
1. Insufficient rigidity
During injection molding, the mold is subject to huge holding pressure. If this pressure causes permanent deformation of the mold, the mold will be unusable, but even within the elastic limit, the deformation generated by the mold can be restored, and when it is deformed The curing and forming of the mold will make it difficult to open the mold, or even unable to open it.When this happens, it is impossible to modify the mold from the structure, but the injection pressure can be appropriately reduced, or the frame can be added from the outside to increase the rigidity. Although it is not good-looking, it is also used.
2. Mould assembly misalignment
If the mold is improperly assembled, such as poor mold alignment, the mold clamping part and its joints are not accurately aligned, which will make the melt filling imbalance and easily cause mold deformation or misalignment.In this regard, the mold should be reassembled. For the imbalance of the mold filling, sometimes the method of correcting the gate can be used to correct it.
(XNUMX) Cavity damage and its removal
The cavity is the place where the molded plastic part is formed. Its damage will directly affect the quality of the product. The cavity damage is the hard damage on the inner surface of the cavity, which causes the surface to produce scratches, pits, cracks and other defects, which are the causes of these damages. And its elimination method is as follows.
1. Hard object damage cavity
Sometimes it is difficult to take out the plastic part after opening the mold, so use a screwdriver and other hard tools to reluctantly take it out, which will easily damage the cavity.In addition, after opening the mold, accidentally dropping a wrench, a hammer, and other hard objects into the cavity, causing damage to the cavity.
2. Improper operation
If the plastic part is not taken out, close the mold, especially in automatic molding, the cured plastic part is easy to damage the cavity and mold.
3. Repair of damage
After the cavity is damaged, it is difficult to continue working without repair. There are several ways to repair the cavity.
- (1) Welding.Welding is a commonly used repair method, and the most commonly used welding method is gas welding.If electric welding is used, because the temperature is too high, the mold is prone to deformation or even cracking. Use electric welding to repair, preheat the mold, and heat treatment after welding.
- (2) Inserts.For small area and deep damage, inserts can be added to repair. Generally, inserts are drilled after drilling. When drilling, be careful not to drill through the cooling water channels and screw holes.The fit between the insert and the cavity should be close, and then grind smoothly after installation.
- (3) Electroplating.For defects with a depth of less than 0.5mm, it is better to repair it by electroplating, which can be plated with copper or chromium.
- (4) Percussion.For cavities with softer materials, drill a blind hole on the back of the damaged part, and then knock the bottom of the blind hole to make the damage bulge; or knock 3mm away from the damage to make the recess bulge. Then grind, grind, and polish the convex part.
(XNUMX) Mold rust and its removal
Injection molds are mostly made of tool steel. During work, it encounters corrosive gases, water and other substances that cause rust.Plastic parts made from rusty molds will cause quality problems, so they need to be eliminated.
1. The gas produced by the decomposition of the melt
Some raw materials will produce volatile gases when heated, and many raw materials will also produce volatile gases when they are overheated. These gases are corrosive and diffuse around the machine. When the mold is not working, they will corrode the mold.In this regard, when the machine stops working, use a soft cloth to clean the mold and close the mold. If it is not used for a long time, the mold cavity should be sprayed with anti-rust agent. mouth.
2. Cooling water in the mold
Cooling water is often used in the mold to wake up and cool, so there is more moisture around the machine.If the mold is cooled to below the dew point, moisture in the air will form water droplets on the surface of the mold. If it is not wiped off in time, it will easily rust.Especially after the mold stops working, condensed water will be generated quickly.Therefore, do not stop molding easily, even if you want to stop, turn off the cooling water and wipe the mold dry.
3. Carbides produced during molding
After the mold works for a long time, carbides are precipitated and decomposed in the molding material, which often causes the mold to wear, corrode or rust.In this regard, if carbide formation is found, it should be wiped off and cleaned with a dry cloth immediately.
To sum up, in order to reduce the production cost of injection molds for the entire enterprise, it is necessary to make a two-pronged effort in the quality of injection molds and subsequent maintenance to increase the service life of the entire injection mold, thereby reducing product costs. Enhance the overall market competitiveness.
Link to this article:What factors affect the quality of injection molds and how to maintain them?