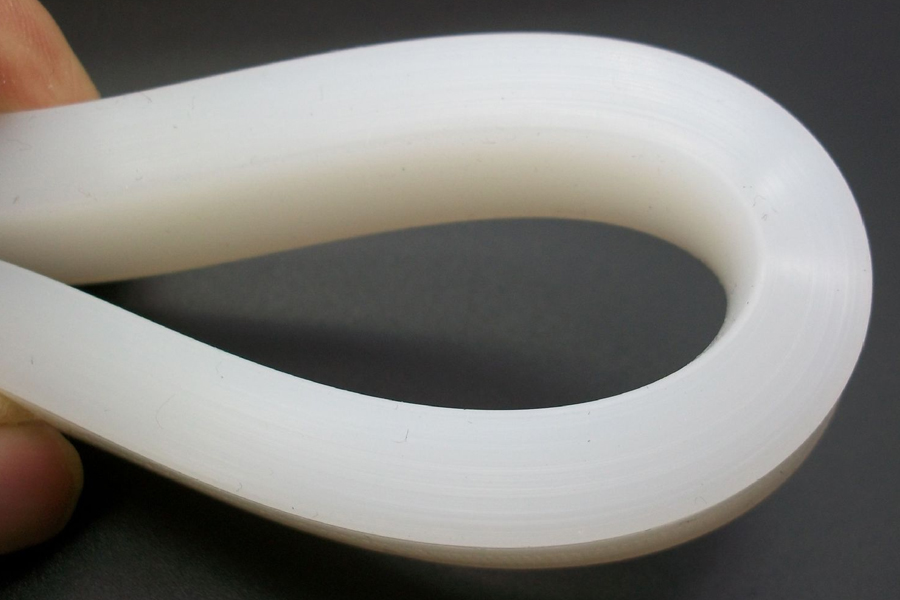
The main reasons for appearance fatigue are as follows: The angle of the plastic mold of the product The main problem of the product is that the angle of the plastic mold of the product is too small, which will cause resistance on the side of the product. Corresponding to the different texture requirements on the product side, we already have relevant experience, and which specifications of the texture surface should have a larger plastic mold angle, most engineers have the judgment.
It is necessary to avoid solving such problems in the early stages of product evaluation. If the customer’s product does not allow enough plastic mold corners, the mold engineer must not take risks, and must consider using other technical means (such as mold mechanism) to avoid this situation. In addition to avoiding product drawing problems, mold design is also very important and must be carefully considered.
Here are some examples to illustrate how mold design avoids damaging the side of the product. In order to deal with the rounded corners of the parting surface, product designers usually input the rounded corners directly when designing the product. In fact, this is an unreasonable design, because the corner of the plastic mold on the contact surface of the rounded corner is close to zero, which is easy to pull out the flower. Then, the mold designer must modify the product to be connected by a broken line and use the software plastic mold analysis to modify it. Plastic mold angle. It is sufficient to modify the mold structure. Here, we will focus on the three-level positioning of the mold. Improper mold positioning design can also cause product misalignment and product deformation when the mold is opened.
Link to this article:Plastic molds also need new patterns to reduce appearance fatigue