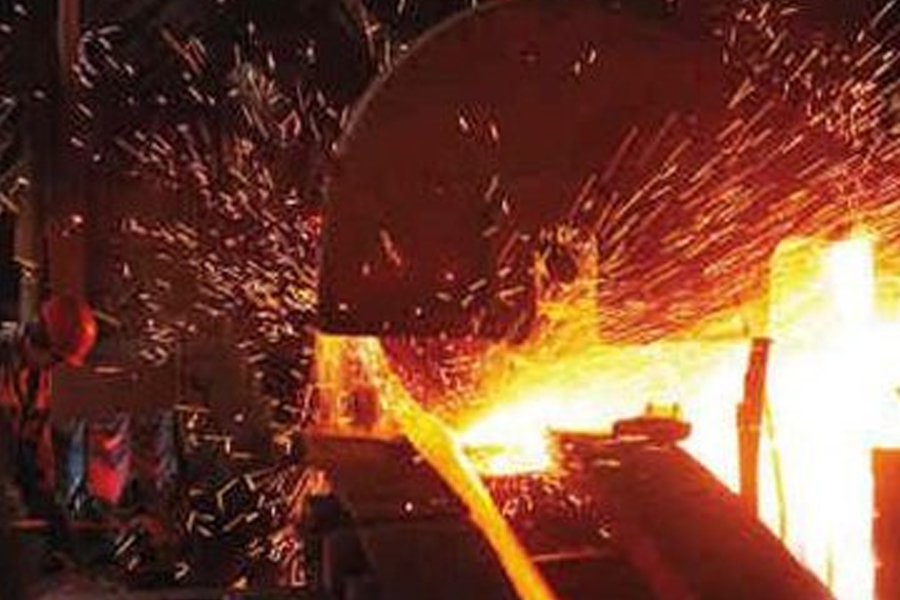
Problems prone to occur in the injection molding process of injection mold products
XNUMX. Why does the injection mold product appear dark and poor in gloss?
Injection mold is a tool for producing plastic products; it is also a tool for giving plastic products a complete structure and precise dimensions.Injection molds often encounter the phenomenon of dark color and poor gloss during the processing and manufacturing process, so what is the reason for the dark color and poor gloss?How to solve it?
In the process of normal injection mold production and processing, the gloss of the mold surface is mainly determined by the type of plastic, the colorant and the finish of the mold surface.The main reasons and solutions for the dark color and poor gloss are as follows.
- 1. Poor finish of the injection mold, rust on the surface of the cavity, and poor mold exhaust.
- 2. Too much recycled materials are used, plastics or colorants are of poor quality, water vapor or other impurities are mixed, and the lubricants used are of poor quality.
- 3. The gating system of the injection mold is defective. The cold slug well should be enlarged, the runner, polished main runner, runner and gate should be enlarged.
- 4. The material temperature and mold temperature are low, and local heating of the gate can be used if necessary.
- 5. Plastics must be fully plasticized, but to prevent degradation of the material, be stable when heated, and adequately cooled, especially for thick-walled ones.
- 6. The clamping force must be sufficient during the manufacturing process of the injection mold.
- 7. The processing pressure of the injection mold is too low, the speed is too slow, the injection time is insufficient, and the back pressure is insufficient, resulting in poor compactness and dark surface.
- 8. Prevent cold material from entering the part, use self-locking spring or lower nozzle temperature when necessary.
Doing the above 8 points can well avoid the phenomenon of dark color and poor gloss in the injection mold. Even if this phenomenon occurs during the production process, remedial measures can be taken to minimize the production progress of the enterprise. The impact of increasing the production efficiency of enterprises.
XNUMX. Why are plastic mold products deformed?
The coordinated changes of the convex and concave molds of the plastic mold and the auxiliary molding system can process a series of plastic parts of different shapes and sizes.In order to meet the needs of molded parts, we need to pay attention to some things when choosing plastic molds and put forward corresponding requirements.To choose a more suitable plastic mold below, you need to meet the following six requirements
- 1. High corrosion resistance Many resins and additives have a corrosive effect on the surface of the cavity. This corrosion causes the metal on the surface of the cavity to be corroded and peeled off, the surface condition deteriorates, and the quality of the plastic parts deteriorates.Therefore, it is best to use corrosion-resistant steel, or chromium plating, cymbal nickel treatment on the surface of the cavity.
- 2. Good wear resistance. The gloss and accuracy of the surface of plastic products are directly related to the wear resistance of the surface of the plastic mold cavity, especially when glass fiber, inorganic fillers and certain pigments are added to some plastics. The plastic melt flows at high speed in the runner and mold cavity together, and has great friction on the surface of the cavity. If the material is not wear-resistant, it will wear out quickly, which will damage the quality of the plastic part.
- 3. Good dimensional stability. During plastic molding, the temperature of the plastic mold cavity must reach above 300°C.For this reason, it is best to select tool steel (heat-treated steel) that has been properly tempered.Otherwise, the microstructure of the material will change, which will cause the size of the plastic mold to change.
- 4. Easy-to-process mold parts are mostly made of metal materials, and some structural shapes are still very complex. In order to shorten the production cycle and improve efficiency, the mold materials are required to be easy to process into the shape and accuracy required by the drawings.
- 5. Good polishing performance. Plastic plastic parts usually require good gloss and surface condition. Therefore, the roughness of the cavity surface is required to be very small. In this way, the surface of the cavity must be surface processed, such as polishing, grinding, etc.Therefore, the selected steel should not contain rough impurities and pores.
- 6. It is less affected by heat treatment. In order to improve the hardness and wear resistance, the plastic molds are generally heat treated, but this treatment should make the size change small.Therefore, it is best to use pre-hardened steel that can be machined.
Link to this article:Problems prone to occur in the injection molding process of injection mold products